关键词: 煤焦油; 减压蒸馏; 新工艺
上海亚荣生化仪器厂生产的旋转蒸发器既能减压蒸馏也能常压蒸馏,煤焦油蒸馏工艺主要有减压蒸馏、常压蒸馏和常减压蒸馏三大类。对于常压蒸馏和减压蒸馏工艺,蒸馏所需的热量主要由1台管式炉提供,受管式炉结构限制,单套加工装置处理能力较低,因此这 2 种工艺主要应用于年处理无水焦油30万t及以下规模的工艺装置。对于常减压蒸馏工艺,焦油馏分在多台蒸馏塔内进行分离,蒸馏所需的热量由多台管式炉分别提供,因此主要应用于年处理无水焦油30万t以上大规模或超大规模的工艺装置。
1 、焦油常压蒸馏和传统减压蒸馏工艺比较
焦油常压蒸馏工艺起源于20世纪60年代,由于具有工艺流程短、设备数量少、基建投资低、设备维护量较少、控制简单、易于操作等优点,是国内焦油加工应用最广泛的焦油蒸馏工艺,该工艺以切取酚油、萘油和洗油三混馏分的流程最为普遍,切取三混馏分的焦油常压蒸馏工艺流程。焦油常压蒸馏工艺在一段蒸发器内完成脱水,在二段蒸发器和馏分塔内完成馏分分离。二段蒸发器顶部用一蒽油馏分打回流,馏分塔顶部用轻油馏分打回流。脱水和蒸馏分离所需的热量全部由1台管式炉提供,管式炉分为对流段、过热蒸汽段和辐射段。为了降低操作温度,二段蒸发器和馏分塔底部通入直接蒸汽,进行汽提以降低沸点。
虽然通入直接蒸汽降低了沸点,但是焦油进入二段蒸发器的一次蒸发温度仍高达380℃左右,这就需要管式炉辐射段焦油出口温度在400℃以上,实际操作过程中管式炉容易结焦。另外通入的直接蒸汽与油品分离后产生的含酚废水难以处理,给工程建设增加环保压力。由1台管式炉提供焦油脱水和馏分分离 2 部分热量,在对流段和辐射段焦油出口温度的控制上,只能保证辐射段焦油出口温度得到有效控制。对于原料焦油含水量符合设计要求且比较稳定的生产装置,生产操作比较容易控制;对于原料焦油含水量偏离设计要求或含水量波动较大的生产装置,会影响装置运行的稳定性,给生产操作增加难度。
2、减压蒸馏工艺
该工艺主要馏分的蒸馏分离是在负压下操作,不需要通入直接蒸汽,蒸馏塔及管式炉出口焦油的温度较低,减轻了炉管的结焦,不产生含酚废水,而且减压操作减少了有毒有害气体的泄漏量,因此在环境保护上有极大的优势。改进的焦油减压蒸馏工艺流程。焦油减压蒸馏工艺中,预脱水塔的作用是脱除原料焦油的大部分水分,脱水塔的主要作用是分离出轻油馏分并脱除剩余水分,主塔是将焦油中的其他组分分离成酚油、萘油、洗油、一蒽油、二蒽油馏分和中温沥青。脱水塔顶部用轻油馏分打回流,主塔为减压操作,主塔顶部用酚油馏分打回流。脱水和和焦油管式炉3台设备分别提供。下图为焦油减压蒸馏工艺流程图。
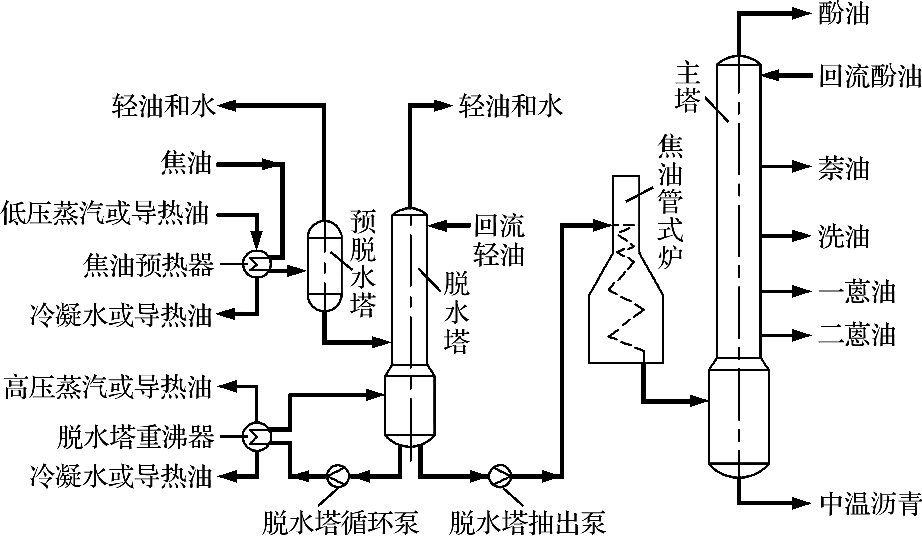
焦油减压蒸馏工艺采用窄馏分切割,与常压蒸馏工艺相比,除增加 1 套真空机组外,换热或冷却器、采出泵等数量也多于焦油常压蒸馏工艺,所以对于相同建设规模,现行的减压蒸馏工艺无论是一次性投资、占地面积还是运行成本都高于常压蒸馏工艺。特别是对于没有高压蒸汽的单位,还需要增加导热油系统,包括导热油炉、循环泵、膨胀槽、贮槽、注入泵等设备,需额外增加几百万的投资。
3、2种工艺比较
通过上述工艺介绍,可以定性的看出焦油常压蒸馏和减压蒸馏工艺的优缺点,下面以处理无水焦油20万 t/a 的焦油蒸馏装置工程设计为例,对 2 种工艺进一步进行定量比较。对于相同建设规模的焦油常压蒸馏和减压蒸馏工艺装置,蒸馏分离所需要的总热量基本相同,Q 1 ≈Q 2 。两者区别在于,常压蒸馏工艺所需热量全部由管式炉消耗燃料气提供,而减压蒸馏工艺热量由焦油预热器、脱水塔重沸器和管式炉分别提供,焦油预热器用低压蒸汽加热,宝钢工程的脱水塔重沸器用高压蒸汽加热,只有管式炉的热量是消耗燃料气提供。因此在人们的认知中,一直认为减压蒸馏工艺燃料气消耗量低于常压蒸馏工艺,所以节能。实际上蒸馏过程需要的热量分为原料升温及蒸发、回流升温及蒸发 2 部分,2 种工艺回流位置和回流物料虽然不同,但回流量基本一样,即 R 1 ≈R 2 ,所以用于回流升温及蒸发的热量差别不大。减压蒸馏工艺降低了操作温度,只是减少了原料升温部分的热量,但是与蒸发热量相比,升温所需的热量只占总热量的一小部分,而且操作温度低,原料的蒸发潜热反而增大,蒸发消耗的热量会增加,所以焦油减压蒸馏工艺比常压蒸馏工艺节能的观点是人们认知的误区。
以上内容仅供大家参考,欢迎大家咨询购买上海亚荣生化仪器厂的仪器。